由于鈦合金產品有高強度和耐腐蝕強等特點,越來越多被人們所重視,因此廣泛應用于國防,航空、航海,核電,石油等領域。下文將為大家介紹一例鈦合金棒材在自動探傷過程中發現的缺陷,并進行解剖的分析全過程。
實例: 2017年8月29日我部在檢測牌號TC4,批號304-170754-34,規格φ80×L;發現一根棒(節號-34)距端頭1000mm處,有一個不連續報警信號,缺陷大小當量為≥φ1.2。檢測設備為美國自動探傷設備,制造商TACTIC。探傷儀器USIP40(GE);探傷標準按AMS 2631D class A1,標準人工傷φ1.2-9dB檢測,對報警處標記位置進行標識。該缺陷截面距離邊部38mm(離棒材幾何中心2mm)。見圖。
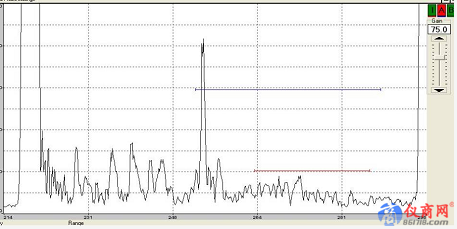
低倍解剖。發現距中心處2mm有明顯亮斑點顯示
圖二、低倍解剖觀察距中心2mm處有明顯亮斑點。
圖三、放大200倍高倍發現缺陷部位有明顯亮斑
在放大200倍觀察,解剖報警處發現亮斑痕跡,亮斑組織和正常組織有明顯差異。但是亮斑處不是引起報警的源頭,因為探傷對偏析的信號響應很弱。
進一步磨拋進行500倍高倍分析解剖部位,將高倍放大到500倍,發現亮斑中心處有微小缺陷,見下圖。
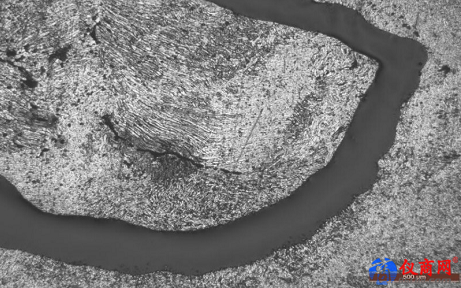
圖四、500倍顯微組織發現微小裂紋。
我們認為該缺陷才是引起探傷儀器報警的信號源。該缺陷粗略分析應該是氣孔,由于在后續的鍛造、精緞加工過程中形變成線狀缺陷。但是最后定性必須以電鏡和能譜分析作為參考依據。
當量大小,由下公式換算:
平底孔和長橫孔換算:
從上面公式可以看出,當檢測φ1.2平底孔換算成橫截面同當量的長橫孔為0.08mm當量。其實我們看到解剖端面缺陷方向正好和探傷檢測方向是垂直,探傷檢測的是長橫孔的孔深面積,而我們解剖的是長橫孔的截面積,孔的直徑為φ0.088mm直徑當量,所以這個裂紋當量相當小,肉眼很難發現。
為了進一步證實缺陷的存在,我們對缺陷部位進行著色滲透探傷,探傷后顯像明顯發現并證明缺陷的存在,而且該缺陷有一定深度。如下圖:
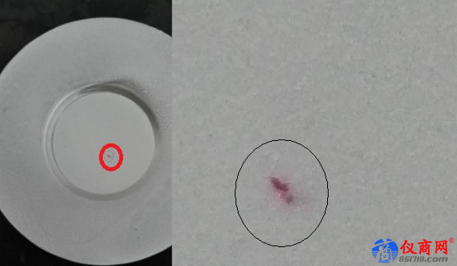